Unlocking Business Potential with Vacuum Forming Silicone Membranes
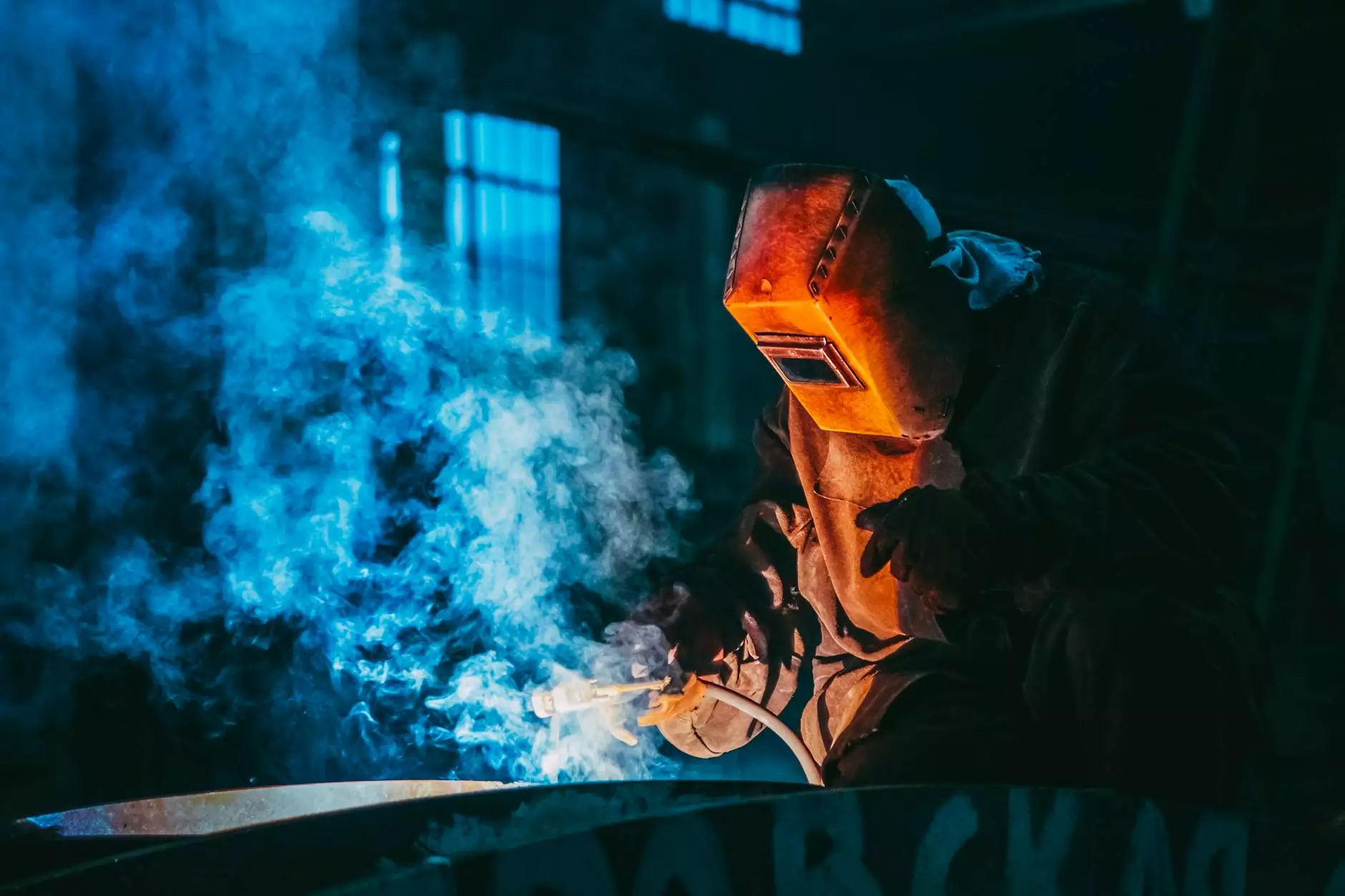
In today's competitive manufacturing landscape, innovation and efficiency are paramount for achieving business success. One of the most transformative technologies driving this progress is the use of vacuum forming silicone membranes. These advanced materials enable manufacturers to produce high-precision, durable, and flexible products that meet the demanding needs of various industries. From automotive to medical, from packaging to electronics, the strategic implementation of silicone membranes can significantly enhance manufacturing quality and productivity.
Understanding Vacuum Forming Silicone Membranes
The vacuum forming silicone membrane is a specialized, high-performance material designed to be used in vacuum forming processes. It acts as a flexible, heat-resistant barrier that molds to complex shapes under the influence of vacuum pressure. This membrane is made from high-quality silicone rubber, renowned for its exceptional durability, chemical resistance, and flexibility.
Unlike traditional plastics or other rubber materials, silicone membranes offer superior temperature tolerance, flexibility over a wide range of frequencies, and excellent inertness, making them ideal for sensitive or intricate production tasks.
Key Characteristics of Vacuum Forming Silicone Membranes
- High Temperature Resistance: Capable of withstanding temperatures up to 250°C (482°F) without degradation.
- Excellent Flexibility and Elasticity: Easily conforms to complex molds and shapes, ensuring high-precision results.
- Chemical and Weather Resistance: Resistant to oils, acids, bases, and UV radiation, making them suitable for harsh environments.
- Longevity and Durability: Designed for repeated cycles without loss of performance, reducing operational costs.
- Non-Toxic and Biocompatible: Safe for applications involving food contact, medical devices, and pharmaceuticals.
The Business Advantages of Integrating Silicone Membranes in Manufacturing
Implementing vacuum forming silicone membranes is a strategic move that can drastically improve your business outcomes. Here are some compelling reasons why:
1. Superior Product Quality and Precision
Silicone membranes enable the production of highly precise and consistent products. Their pliability and conformity to complex molds result in detailed surface features and tight tolerances. For businesses focused on high-end markets such as aerospace or medical devices, this translates into competitive advantage.
2. Increased Production Efficiency
By leveraging silicone membranes' rapid cycle times and durability, manufacturers can increase throughput while minimizing downtime. The membranes' resistance to wear and tear ensures fewer replacements, leading to optimized manufacturing flow.
3. Cost Savings and Reduced Waste
High-quality silicone membranes have long service lives, reducing recurring material costs. Their ability to produce close-fit molds reduces the need for rework and material waste, significantly lowering operational expenses over time.
4. Versatility Across Industries
Business opportunities expand when utilizing versatile materials. Silicone membranes are suitable for applications like vacuum-assisted molding, sealing, testing, and even biomedical applications, opening pathways to diverse markets.
Applications of Vacuum Forming Silicone Membranes in Modern Industries
The wide-ranging applications of vacuum forming silicone membrane underscore its importance in contemporary manufacturing. Here are some key sectors benefiting from this technology:
Automotive Industry
Silicone membranes are used in the production of custom gaskets, seals, and dashboard components. Their ability to withstand high temperatures and harsh chemicals makes them essential for engine and interior parts.
Medical and Healthcare
In medical device manufacturing, silicone membranes serve as protective barriers, diaphragms, or sealing elements. Their biocompatibility and inertness are critical for patient safety and compliance with strict industry standards.
Electronics and Electrical Equipment
These membranes are employed as insulating layers, protective seals, or flexible connectors in electronic devices, ensuring performance and safety in sensitive equipment.
Packaging and Consumer Goods
Silicone membranes contribute to high-quality packaging solutions, providing flexible, heat-resistant liners and seals that extend the shelf life and integrity of products.
Aerospace and Defense
Their durability under extreme conditions makes silicone membranes suitable for sealing, insulation, and shielding components in aerospace applications.
How to Choose the Right Silicone Membrane for Your Business
When sourcing vacuum forming silicone membranes, it’s crucial to consider various factors to ensure optimal performance and value:
Material Quality and Certifications
Always select membranes produced by reputable suppliers who adhere to strict quality standards and hold relevant certifications such as ISO, FDA, or UL. High-quality membranes ensure safety, durability, and compliance.
Temperature Range and Chemical Resistance
Match the membrane’s specifications to your application’s environmental conditions. For high-temperature processes, opt for membranes with better heat tolerance; for chemically aggressive environments, prioritize chemical resistance.
Size, Thickness, and Customization Options
Determine the dimensions and thickness that suit your molds and production volume. Many suppliers offer customization services to optimize the fit and performance.
Cost and Lead Time
Balance quality with budget constraints. Choose suppliers who can deliver promptly and provide cost-effective solutions without compromising quality.
Leading Suppliers and How to Source Premium Silicone Membranes
For businesses aiming to maximize their production potential, sourcing from a trusted rubber membrane shop is essential. Reputable suppliers offer:
- Comprehensive product catalogs featuring various silicone membranes tailored for vacuum forming
- Expert technical support to guide your selection process
- Customized solutions for specific industrial needs
- Competitive pricing and reliable delivery schedules
- Samples and testing options to validate suitability before large-scale purchase
Innovating Your Business with High-Quality Silicone Membranes
Incorporating vacuum forming silicone membranes into your manufacturing processes offers a strategic advantage by enhancing product quality and operational efficiency. By choosing the right membranes and supplier, your business can:
- Expand into new markets with innovative, high-precision products
- Reduce production costs through durability and efficiency
- Meet stringent industry standards for safety, cleanliness, and performance
- Build a reputation for quality and reliability among clients and partners
- Stay ahead in the rapidly evolving manufacturing landscape
Conclusion: Elevate Your Business with the Power of Silicone Membranes
The success of modern manufacturing industries hinges on the adoption of advanced materials and processes. Vacuum forming silicone membranes are a vital component that empowers businesses to produce complex, high-quality products while optimizing costs and efficiency. By investing in top-tier silicone membranes from established suppliers like silicone-membranes.eu, companies can unlock new levels of innovation, meet growing market demands, and establish a formidable competitive edge.
Embrace the future of manufacturing with silicone membranes — where durability, flexibility, and performance converge to redefine what your business can achieve.