Unlocking the Power of Prototype Mold in Metal Fabrication: The Key to Innovation and Precision
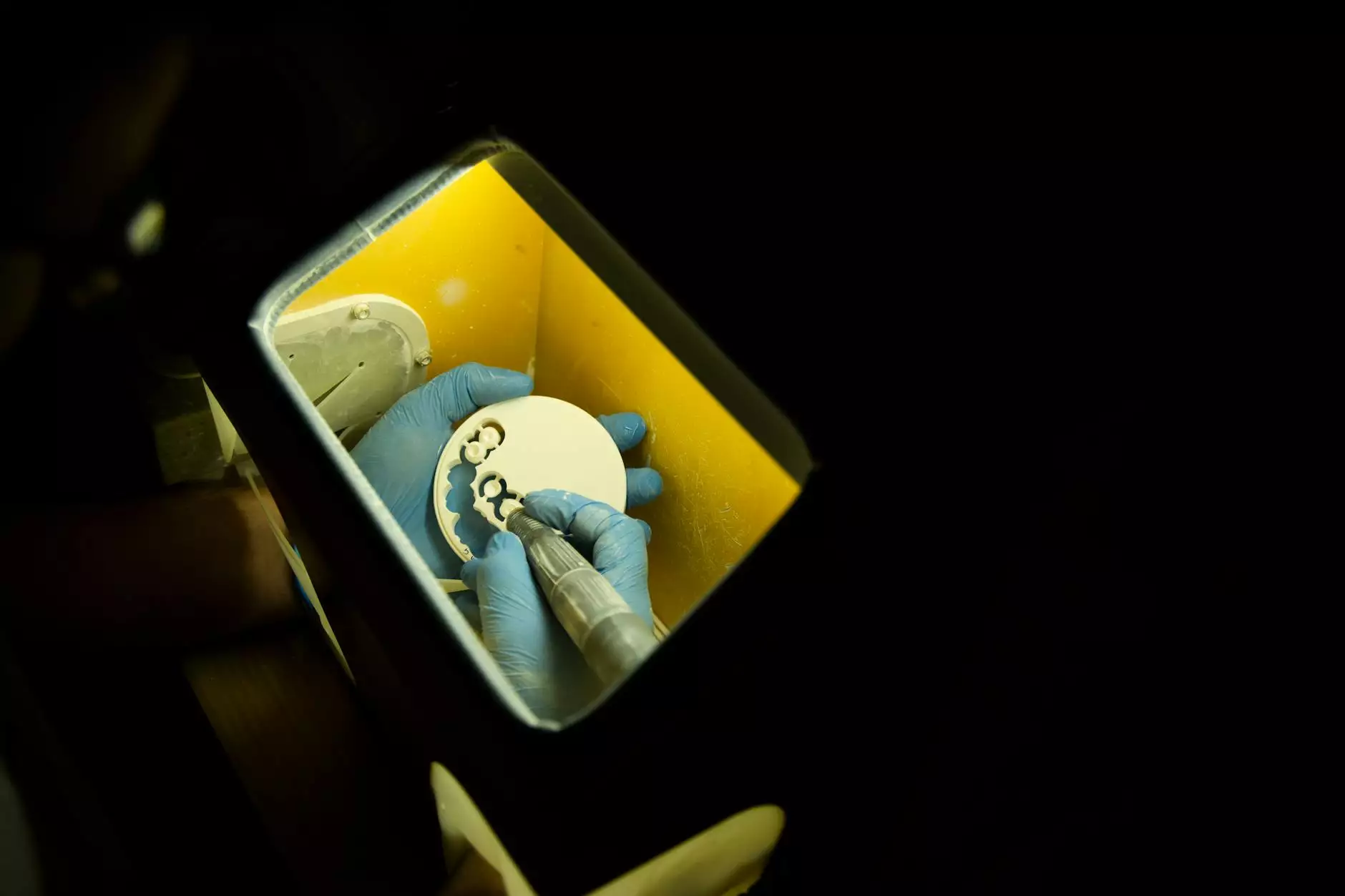
In today's highly competitive manufacturing environment, the ability to rapidly develop, test, and refine product designs is crucial for success. Central to this process is the creation of prototype molds, which serve as the foundational tools enabling metal fabricators to produce initial versions of products with exceptional accuracy and efficiency. As a premier metal fabricator at DeepMould.net, we emphasize the importance of high-quality prototype molds in transforming ideas into tangible, functional prototypes that pave the way for full-scale manufacturing.
Understanding the Role of Prototype Mold in Metal Fabrication
Prototype molds are specialized tools used to cast or form initial versions of a product, allowing engineers and designers to assess form, fit, and function before moving to mass production. They are typically crafted with precision materials tailored to match the final product specifications, but often with variations that expedite the development process. These molds are pivotal for testing design concepts, verifying manufacturing processes, and identifying potential issues early, which ultimately saves time and reduces costs.
The Significance of Prototype Mold in Accelerating Product Development
Speed is of the essence in today’s fast-paced market. The strategic use of prototype molds enables companies to:
- Shorten development cycles: Rapid prototyping allows for quick iterations, enabling design adjustments in real-time.
- Enhance design accuracy: Physical models provide tangible feedback that digital simulations alone cannot offer.
- Reduce manufacturing costs: Early detection of potential flaws prevents expensive reworks in later stages.
- Improve stakeholder communication: Visual and tactile prototypes facilitate clearer understanding among teams, investors, and clients.
Types of Prototype Molds in Metal Fabrication
The choice of prototype mold depends on factors such as material, complexity of the part, and intended use. Here are some common types:
- Aluminum Prototype Molds: Lightweight, cost-effective, ideal for low-volume production and early-stage testing.
- Steel Prototype Molds: Durable and capable of withstanding multiple cycles, suitable for more detailed testing and small batch production.
- Silicone and Rubber Molds: Useful for flexible or intricate designs, often used for visual prototypes or soft material testing.
Materials and Technologies in Prototype Mold Manufacturing
The quality and precision of prototype molds hinge on the materials and manufacturing technologies employed. Leading metal fabricators utilize advanced equipment such as CNC milling, EDM (Electrical Discharge Machining), and additive manufacturing to produce highly detailed molds.
Materials commonly used include:
- High-Speed Steel (HSS): Offers excellent machinability and wear resistance, suitable for durable prototypes.
- Aluminum Alloys: Provide ease of machining and lightweight features, ideal for rapid prototyping.
- Specialized Alloys: Such as tool steels for more complex, high-precision applications.
Design Considerations for Effective Prototype Molds
Successful prototype mold creation requires meticulous planning and detailed design. Below are critical considerations:
- Accuracy of Dimensions: Ensuring the mold precisely replicates the final product specifications.
- Material Compatibility: Selecting materials that match the end-use environment and manufacturing process.
- Ease of Repair and Modification: Designing molds that facilitate adjustments, saving time during iterations.
- Surface Finish: Achieving the desired surface quality to accurately simulate the final product appearance.
The Manufacturing Process of Prototype Molds
The journey from concept to a finished prototype mold involves several stages:
1. Conceptual Design and CAD Modeling
Using sophisticated computer-aided design (CAD) software, engineers develop detailed mold drawings, incorporating all necessary features and tolerances.
2. Material Selection and Preparation
Based on the specifications, suitable materials are chosen and prepared for machining or casting.
3. Precision Machining
Advanced CNC machines and EDM are employed to craft the mold, ensuring high accuracy and surface quality.
4. Assembly and Testing
The various mold components are assembled, and trial runs are conducted to verify functionality and fit.
5. Modification and Refinement
Based on testing feedback, necessary modifications are made to optimize the prototype mold.
Quality Assurance in Prototype Molds
High standards of quality assurance (QA) are vital for producing reliable prototype molds. This includes rigorous inspections, dimensional metrology, and surface analyses to verify that each mold meets exact specifications. Employing techniques such as 3D scanning and non-destructive testing ensures that the final prototype mold is flawless and ready for its intended purpose.
The Strategic Advantage of Choosing DeepMould.net for Your Prototype Mold Needs
At DeepMould.net, we specialize in delivering custom prototype molds tailored to your specific project requirements. Our team of experienced engineers and skilled technicians leverage cutting-edge technology and premium materials to produce prototypes that empower your business to innovate faster, cut costs, and maintain a competitive edge.
Our core advantages include:
- Advanced Manufacturing Capabilities: CNC, EDM, additive manufacturing, and more for high-precision molds.
- Fast Turnaround Times: Streamlined processes ensure rapid delivery without compromising quality.
- Cost-Effective Solutions: Competitive pricing with the flexibility to handle both small and large volume projects.
- Expert Consultation: Guidance throughout the design, material selection, and manufacturing phases.
Transforming Your Ideas into Reality with High-Quality Prototype Molds
Investing in top-tier prototype molds is a strategic move that can dramatically enhance your product development cycle. By meticulously designing, manufacturing, and testing prototypes, your business can identify potential flaws early, optimize design features, and streamline final production processes. This proactive approach reduces waste, accelerates time-to-market, and ultimately increases profitability.
Future Trends in Prototype Mold Manufacturing and Metal Fabrication
The industry is continuously evolving, with innovations such as:
- Additive Manufacturing: Enabling complex, lightweight, and highly detailed prototype molds.
- Smart Molds: Incorporating sensors for real-time monitoring and feedback during testing.
- Material Advancements: Development of new alloy compositions that offer even better performance and durability.
- Automation and AI: Streamlining mold design and manufacturing processes through intelligent algorithms.
Conclusion: Elevate Your Product Development with Superior Prototype Molds
In summary, prototype molds are the cornerstone of innovative and precise metal fabrication. They provide invaluable insights into product design, embody the first physical representation of your concepts, and set the stage for successful mass production. Partnering with a reputable and experienced manufacturer like DeepMould.net ensures that your prototypes are crafted with excellence, leveraging the latest technology, materials, and engineering expertise. Embrace the future of manufacturing today by investing in quality prototype molds—the critical first step toward bringing your visionary ideas to life.