Mould Tooling Design China: Innovations and Advancements
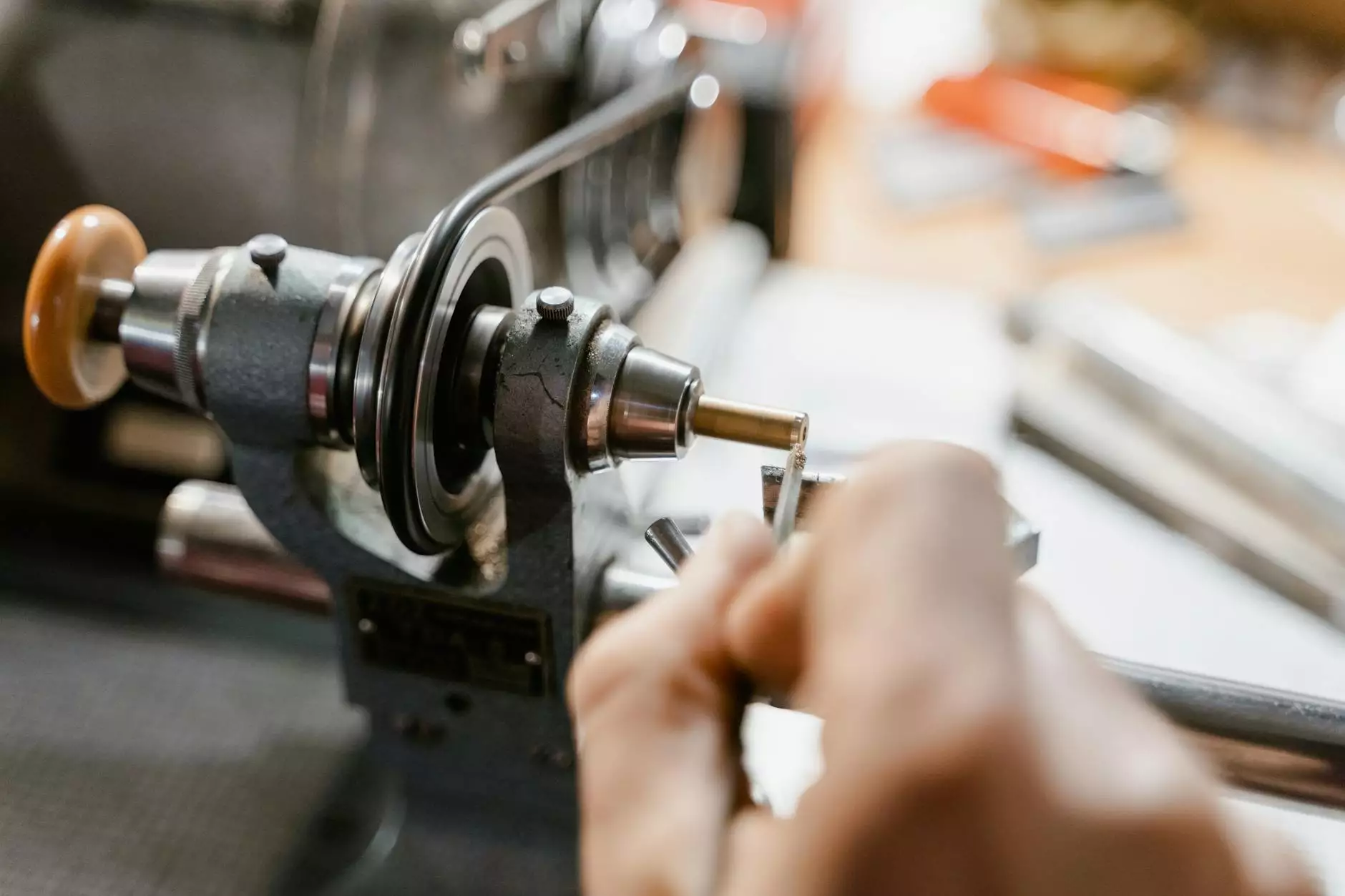
Mould tooling design has become a pivotal part of modern manufacturing, particularly in China, which has established itself as a global leader in this field. Mould tooling design China refers to the processes and technologies used in creating the molds that are fundamental for producing various parts in numerous industries, including automotive, consumer electronics, and household appliances.
The Importance of Mould Tooling Design
The significance of effective mould tooling design cannot be overstated. It directly impacts production efficiency, quality of final products, and overall manufacturing costs. Companies like DeepMould exemplify excellence in this area, pushing the boundaries of what is possible in metal fabrication and mould design.
Key Benefits of High-Quality Mould Tooling Design
- Enhanced Product Quality: Precision in design ensures that the manufactured parts meet stringent quality standards.
- Cost Efficiency: Well-designed tools reduce waste and improve the speed of production.
- Faster Time to Market: Streamlined production processes allow businesses to bring their products to market more quickly.
- Innovation Opportunities: Advanced tooling designs enable the development of complex geometries that can lead to innovative product solutions.
Understanding the Mould Tooling Design Process
The process of mould tooling design is intricate and requires comprehensive planning and execution. It typically involves several stages:
1. Conceptual Design
During the conceptual design phase, engineers and designers collaborate to understand the product requirements and design the initial concepts. This phase includes:
- Defining product specifications
- Creating preliminary sketches
- Deciding on materials
2. Detailed Design
Once the concept is approved, the detailed design phase begins. This involves creating precise CAD (Computer-Aided Design) models that specify every detail of the mold, including dimensions, tolerances, and surface finishes.
3. Prototyping
Prototyping is crucial as it allows for the testing of the design before mass production. This phase includes the following steps:
- 3D printing of the initial mold
- Conducting tests for functionality and structural integrity
- Making necessary adjustments based on test results
4. Tool Making
After finalizing the design, the next step is tool making, where the actual molds are produced using high-precision machinery. Innovations in this area, such as CNC machining and EDM (Electrical Discharge Machining), have significantly improved the accuracy and efficiency of the process.
5. Production
Finally, the molds are used in production. Continuous monitoring and quality checks are performed to ensure that the products meet the required specifications.
Technological Innovations in Mould Tooling Design China
China is at the forefront of technological advancements in mould tooling design. Here are some of the latest innovations:
Automation and Robotics
Automation has revolutionized the mould tooling process. Robotic arms and automated machinery can perform repetitive tasks with high efficiency and minimal errors. This not only speeds up production but also reduces labor costs.
Advanced Materials
China has been investing heavily in the research and development of new materials which improve the durability and heat resistance of moulds. Materials such as high-speed steels, alloys, and advanced polymers are now commonly used in the industry.
Digital Twin Technology
This innovative technology allows manufacturers to create a virtual twin of the physical mold. By simulating how the mold will behave under different conditions, manufacturers can anticipate potential issues and optimize the design before production.
Challenges in the Mould Tooling Industry
Despite the advancements, several challenges still persist:
1. Maintaining Quality Standards
As competition grows, meeting international quality standards becomes increasingly important. Ensuring that every mold produced adheres to these standards is essential for customer satisfaction and retention.
2. Rising Material Costs
The cost of raw materials can fluctuate dramatically, impacting the overall cost of mould tooling design. Manufacturers must find a balance between cost, quality, and sustainability.
3. Skilled Labor Shortage
As technology advances, the demand for skilled labor increases. Companies must invest in training programs to ensure that their workforce is equipped to handle the latest technologies and methodologies in the industry.
The Future of Mould Tooling Design China
Looking ahead, the future of mould tooling design in China appears bright. With ongoing investments in technology and an emphasis on quality and efficiency, Chinese manufacturers are likely to maintain their competitive edge in the global market. Here are a few trends that may shape the future:
1. Increased Use of AI and Machine Learning
Integrating AI into the design and production processes can lead to smarter decision-making, reducing human error, and optimizing resources.
2. Sustainability Practices
As global awareness of environmental issues grows, the demand for eco-friendly manufacturing processes will increase. Companies that adopt sustainable practices in their mould tooling design will likely have a competitive advantage.
3. Global Collaboration
Collaboration between Chinese manufacturers and global companies can lead to shared knowledge, better practices, and more innovative solutions, further enhancing the quality and efficiency of mould tooling designs.
Conclusion
In conclusion, mould tooling design China is an evolving field that is essential to the global manufacturing landscape. With advancements in technology, a focus on quality, and a commitment to overcoming challenges, Chinese manufacturers are setting new standards for the industry. As we move into the future, embracing innovation and collaboration will be key to sustaining growth and maintaining a competitive edge.
Whether you are looking for advanced mould designs or seeking to understand the intricacies of the manufacturing process, partnering with industry leaders such as DeepMould can provide the expertise and support needed for success in today's competitive market.